MENU
RecurDyn Simulation of Windshield Wiper System
RecurDyn: Ideal When Flexibility of Every Component Influences Overall System Behavior
RecurDyn is the ideal software for simulating windshield wiper systems, because the system is a mechanism in which the flexibility of every component affects the behavior of the entire system. Shown below is a simulation of snow or ice blocking the wiper blades. If the blockage occurs low enough on the windshield, the wipers blades will hit the blockage but the motor will continue through its rotation, causing a deformation of the wiper system distributed across every component. In order to calculate the motor torque as well as the internal stresses of each component, the flexibility of every component must be modeled accurately. Shown below is an overall view of Von Mises stress during the simulation of ice blockage.
Video 1: RecurDyn simulation of windshield wiper system being blocked by snow or ice. Von Mises stress contour plots are displayed.
RecurDyn/FFlex Simulates Nonlinear Deformation and Contact with Flexible Bodies
Shown below is a close-up view of some of the Von Mises stresses occurring throughout the system. Here, RecurDyn/FFlex (Full Flex) is being used to include the entire Finite Element (FE) mesh in the model. With this approach, local stresses are accurately modeled. Nonlinear deformation as well as contact with the flexible bodies can also be modeled.
Video 2: Detailed view of Von Mises stress in windshield wiper system components as windshield wipers are blocked.
Simulating Multiple Blocking Angles to Obtain Critical Stall Angle
Models can be easily set up to simulate multiple blocking angles, measuring the maximum motor torque at each angle. As shown below, the blocking bodies rotate through a range of 20-30 deg (measured at the crank), at intervals of 2 deg. At each blocking interval, the crank initially moves along with the blocks, and then rotates back against the blocks to test the wiper system.
Video 3: Simulation of windshield wiper system being blocked at multiple crank angles.
For any given maximum motor torque, the critical stall angle can be determined from the multiple-blocking-angle simulation shown above. First, the peak motor torque at each blocking angle is measured. From this, a curve of required motor torque vs. blocking angle can be generated. Interpolation along this curve can yield the critical stall angle for any given maximum motor torque, as shown below.
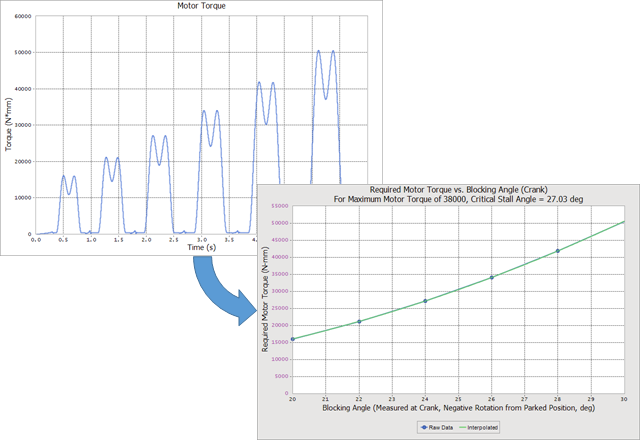
Figure 1: Plot of motor torque during multiple-blocking-angle simulation, yielding plot of required motor torque vs. blocking angle, which can yield the critical stall angle for any given maximum motor torque.
Blockage of Driver- or Passenger-Side Only
Other blocking configurations such as the blockage of only the driver- or passenger-side wiper can also be simulated. In the model being shown here, a parametric setting has been created to enable easy selection of the blocking configuration.
Video 4: Driver side wiper blocked at multiple angles.
Video 5: Passenger side wiper blocked at multiple angles.
Conclusions
- RecurDyn is the ideal simulation tool for evaluating windshield wiper system designs.
- Modeling all the bodies of a wiper system as flexible is necessary for accurate results.
- The flexibility of each component will influence the loads exerted on the others.
- RecurDyn/FFlex can efficiently simulate flexible bodies going through large deflections and deformations.
- The entire mesh for each body is easily imported into RecurDyn.
- Users don’t need to run separate modal analyses for each component and then import the results.
- Nonlinear deformation can be simulated.
- Accurate local stresses can be obtained.
- Contact with flexible bodies can be simulated.
- RecurDyn models can be parameterized to run complex simulations.
More Information
- Learn about RecurDyn/FFlex (Full Flex) which was used to model the flexible bodies in this system.